FlexiForce : les 6 phases de l'intégration
Les secrets d'une intégration réussie des capteurs FlexiForce
Comment le capteur va-t-il se comporter dans mon application ?
Moteurs de l'innovation, les ingénieurs s'appuient sur leur formation, leur expérience et leur instinct pour faire des choix importants dans leurs démarches de conception. Chaque technologie embarquée présente des propriétés inhérentes et des nuances uniques. Et les décisions prises en début de processus peuvent avoir un impact majeur par la suite. Disposer d'un cadre établi peut aider à structurer le projet et à réduire le risque d'erreurs coûteuses et fastidieuses.
Prenons l'exemple des capteurs de force fins et flexibles. Les consommateurs exigeant des appareils plus petits et plus élégants, de plus en plus de concepteurs se tournent vers les capteurs FlexiForce™ en raison de leur légèreté, de leur adaptabilité et de leur faible consommation. Bien que le développement d'un appareil, de sa conception à son achèvement, suive un chemin unique, nous avons identifié six phases principales, ou points de contrôle, que les ingénieurs doivent valider.
Une équipe de conception souhaitait développer une pompe d'administration de médicaments automatisée et portable de nouvelle génération. Ils avaient besoin d'un capteur capable, non seulement de détecter toute dilatation d'un tube à l'intérieur du dispositif, mais aussi de tenir dans un espace très restreint. Nous avons suivi l'équipe pendant qu'elle naviguait à travers ces six phases de conception et nous avons compilé leurs expériences suite aux challenges qu'ils ont rencontrés tout au long du processus.
Dans la phase 1, celle de la caractérisation du capteur, les ingénieurs qui conçoivent avec les capteurs FlexiForce cherchent à répondre aux questions suivantes :
- Quelle sont la fonction et la caractéristique fondamentale du capteur FlexiForce ?
- Comment réagit le capteur FlexiForce avec les circuits et les interfaces mécaniques que nous envisageons pour cette application ?
Cette équipe de conception en particulier avait besoin d'un plan de caractérisation de capteur. Plutôt que de concevoir un montage de chargement et de créer des circuits à partir de zéro, ils ont utilisé un kit de caractérisation de capteur FlexiForce pour rationaliser le processus. Le kit comprend une cellule de charge étalonnée intégrée au dispositif de mise sous contrainte, permettant de disposer d'une référence expérimentale à comparer à la sortie du capteur FlexiForce. Il s'agit d'un élément important de la caractérisation, car il permet aux utilisateurs de bien comprendre les possibilités et les performances du capteur dans des conditions connues. Ces données s'avéreront précieuses dans les phases de conception ultérieures, en fournissant une base de référence pour la mise au point, le dépannage ou le déboguage.
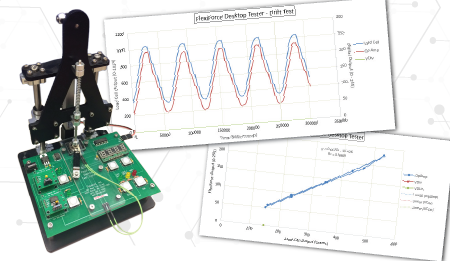
Les développeurs ont commencé en installant le capteur FlexiForce dans le circuit, puis ils l'ont sollicité à la force et à la fréquence requises. Ils ont surveillé la sortie brute du capteur à partir de l'interface Microview. À leur grande surprise, l'équipe a constaté que la sortie du capteur variait selon les différents types de circuits, et en cas de changement du matériau d'interface. Après quelques séries de tests, ils ont opté pour un montage diviseur de tension.
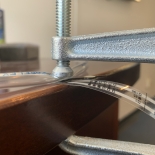
Conception de POC et validation
Dans le premier article de notre série sur les 6 phases de l'intégration des capteurs FlexiForce, nous avons observer que chaque application présente des nuances propres et qu'il n'existe pas de méthode d'intégration unique. Cependant, suivre un schéma standard et se servir d'outils spécifiques peut aider à mieux structurer le processus et à réduire le risque d'erreurs. Nous avons donc abordé la phase 1 de caractérisation des capteurs. Dans ce billet, nous avons présenté l'approche adoptée par une équipe de conception pour recueillir des données sur le comportement du capteur FlexiForce avec les circuits et les interfaces matérielles qu'elle envisageait pour son dispositif médical portable. Les données collectées pendant cette période les ont confortés dans leur choix de circuits.
Cette fois, nous suivons l'équipe qui passe à la phase 2 : la validation du concept. Lors de cette étape, les ingénieurs doivent vérifier la capacité du capteur FlexiForce et de la configuration électrique/mécanique qu'ils ont sélectionné à réaliser la mesure prévue dans une modélisation représentative de leur application.
La finalité du capteur dans cette application est de détecter l'occlusion dans une pompe à insuline. L'équipe a conçu un concept dans lequel le capteur FlexiForce est placé sous un tube en plastique composé d'un matériau similaire à celui qui sera utilisé dans le produit final.
En utilisant un kit de prototypage FlexiForce, les ingénieurs ont pu tester efficacement le capteur dans leur concept en utilisant :
- Un module de circuit analogique diviseur de tension qu'ils ont sélectionné pendant la phase de caractérisation
- Un concentrateur de charge en polycarbonate
- Un logiciel libre, qui a permis de contrôler la mesure de force en direct
Avec cet outil, les concepteurs ont constaté que la tension de référence actuelle du circuit ne fournissait pas une sensibilité suffisante pour obtenir une mesure satisfaisante de l'événement d'occlusion. Ils ont pu facilement augmenter la tension de référence de 0,5 V à 1,0 V en utilisant le cavalier sur la carte du kit de prototypage FlexiForce. Ce réglage a permis de bénéficier des sensibilité et résolution accrues nécessaires pour capter de manière fiable l'occlusion dans le tube.
Après de nouveaux tests, l'équipe a également déterminé que le concentrateur en polycarbonate ne fournissait pas le rendement souhaité et a opté pour un substrat en acier inoxydable.
Maintenant qu'elle a prouvé le concept, l'équipe est prête à passer à la prochaine phase de conception.
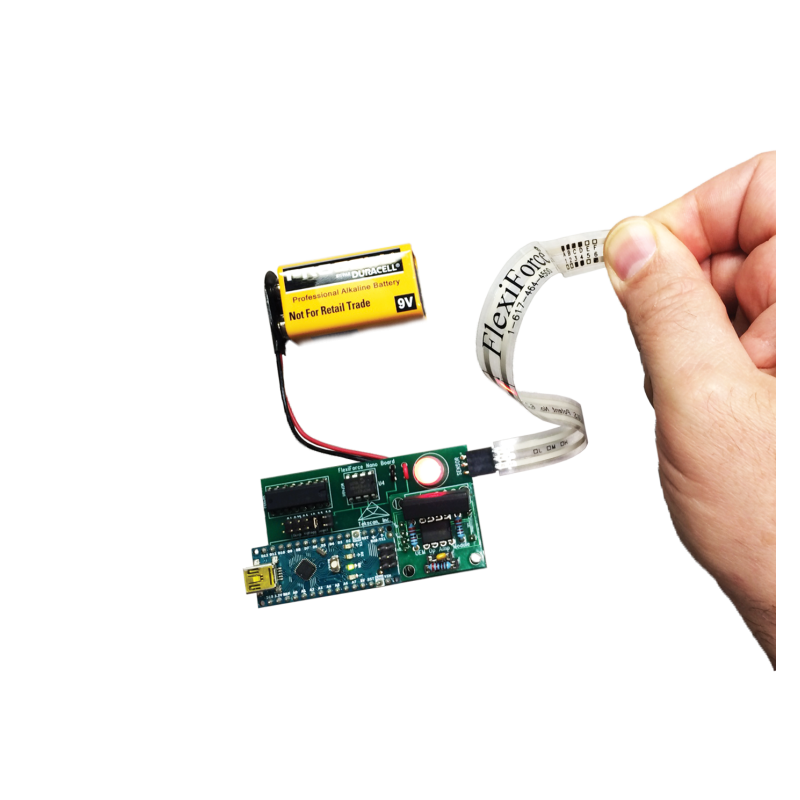
Prototypage
Cet article est le troisième d'une série qui suit le parcours d'une équipe de conception qui a intégré des capteurs FlexiForce dans un dispositif médical afin de détecter une occlusion dans le mécanisme d'une pompe. Lors de l'intégration de composants comme les capteurs de force FlexiForce, suivre un schéma standard et se servir d'outils spécifiques peut aider à mieux structurer le processus et à réduire le risque d'erreurs. Les articles précédents de cette série ont abordé l'approche de l'équipe concernant la caractérisation du capteur et la validation du concept. À ce stade, d'une part, l'équipe a évalué la performance du capteur FlexiForce avec le circuit retenu et, d'autre part, elle a vérifié qu'elle pouvait obtenir les mesures souhaitées à l'aide d'une modélisation de l'application. Il est maintenant temps de passer à la phase 3 : le prototypage.
Au cours de cette phase, les ingénieurs doivent répondre aux questions suivantes :
- Comment allons-nous étalonner le capteur ?
- Le capteur captera-t-il la mesure nécessaire avec la fiabilité nécessaire lorsqu'il sera intégré dans un prototype fonctionnel ?
Le prototype Alpha était constitué du boîtier de la pompe, du tube d'alimentation en fluide, du capteur intégré et du module de circuit analogique diviseur de tension utilisé dans les phases de caractérisation et de validation du concept.
Grâce à la linéarité du circuit choisi lors de la phase de caractérisation du capteur et aux ajustements apportés lors de la phase de validation du concept, les concepteurs ont mis au point une procédure d'étalonnage simple en deux points à l'aide du kit de prototypage FlexiForce. En réalité, l'équipe est retournée au dispositif de chargement du kit de caractérisation FlexiForce pour appliquer des charges connues au capteur et aux matériaux d'interface choisis pour l'étalonnage.
À partir de là, ils ont pu tester le fonctionnement du capteur en faisant couler un fluide dans le tube et en surveillant le retour d'information sur un écran de contrôle. Le capteur ayant été caractérisé et le concept démontré avec la même configuration de circuits et de matériaux au cours des phases précédentes, l'équipe a été en mesure de résoudre tout problème de performance imprévu grâce à ses données de référence.
Une fois satisfaite des performances du capteur dans le prototype Alpha, un prototype Beta a été fabriqué par l'équipe en utilisant le même boîtier et le même tube, ainsi que le reste des composants IHM prévus au projet (écran numérique, cadrans, boutons, etc.). Cette version du prototype incorporait la première version de la carte de circuit imprimé (PCB). Pour concevoir l'interfaçage du capteur, l'équipe a pu utiliser les schémas de circuit analogique mis à leur disposition ce qui lui a permis d'intégrer avec certitude le même circuit sur son PCB.
Dépannage de la sortie du capteur
Lors de la finalisation du prototype bêta, les données émises par le capteur n'étaient pas stables. La sortie du capteur n'était pas répétable compte tenu de la charge cyclique constante supposée appliquée au capteur. L'équipe est revenue en arrière et a comparé les données recueillies dans le prototype alpha aux données de répétabilité recueillies pour le même capteur et le même circuit dans le dispositif de chargement du kit de caractérisation FlexiForce. En examinant les données collectées lors du test de répétabilité pendant la phase de caractérisation, les ingénieurs étaient convaincus que le capteur produirait une sortie répétable avec leur chargement répétable. Ils ont donc examiné l'assemblage de la tubulure dans le prototype pour voir si elle fournissait une force constante au capteur. Ils ont découvert que le tube était configuré de telle sorte qu'il pouvait légèrement se déplacer par rapport au capteur au cours de l'utilisation, ce qui était la cause probable des données erratiques qu'ils observaient. L'assemblage maintenant le tube en place a été modifié de sorte qu'il reste en contact avec le capteur. Le prototype a ensuite été finalisé et présenté à la direction du produit pour approbation finale.
Essais en conditions réelles
Cet article est le quatrième d'une série qui suit l'expérience d'une équipe au cours de l'intégration du capteur FlexiForce dans un dispositif médical pour identifier une occlusion dans le mécanisme d'une pompe. Les articles précédents de cette série ont traité de la méthodologie adoptée par l'équipe pour les phases de caractérisation du capteur, de validation du concept et de prototypage. À cette étape, l'équipe a développé un prototype probant qui lui a donné confiance dans le fait que le capteur FlexiForce est capable de relever de manière fiable la mesure souhaitée dans le dispositif.
Il s'agit maintenant de passer à la phase 4 : Application et tests sur le terrain.
Cette phase requiert la création de plusieurs prototypes destinés à tester les performances, la longévité et la répétabilité. L'objectif de l'équipe est maintenant de prouver que la conception fonctionnera comme prévu sur le terrain tout au long du cycle de vie du produit. Il s'agit d'une phase critique car le produit doit être soumis à l'approbation d'une tierce partie.
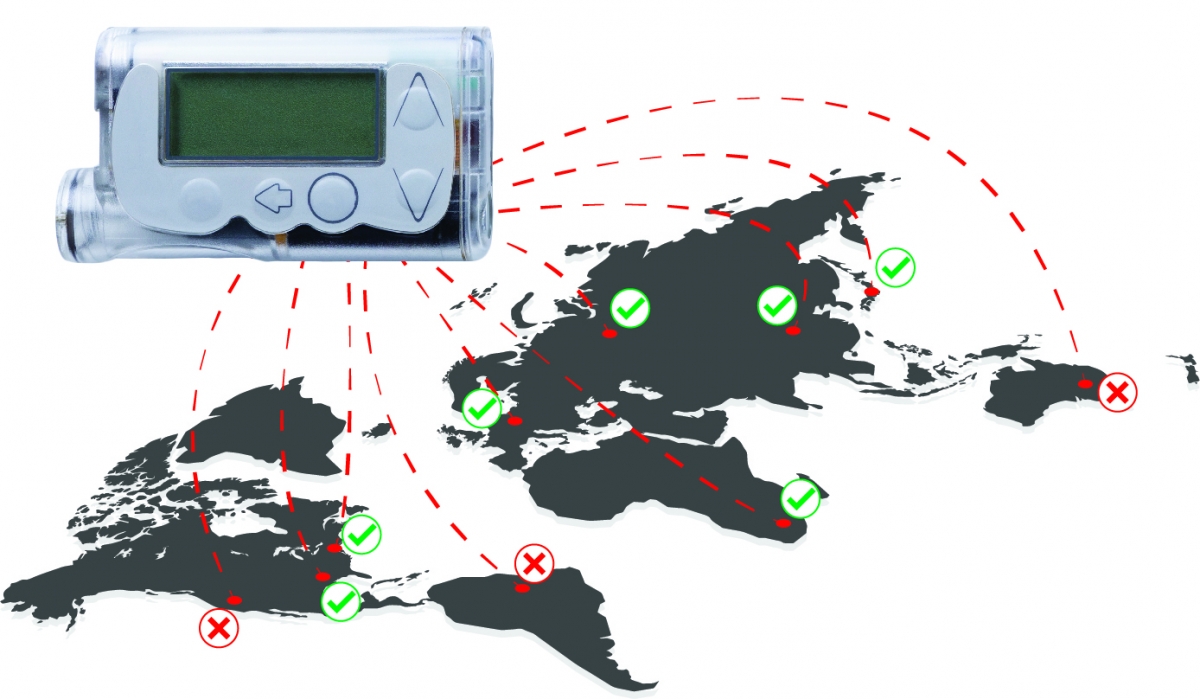
Au cours de cette phase, les ingénieurs cherchent à répondre aux questions suivantes :
- Le déploiement sur le terrain nécessite-t-il des considérations de conception supplémentaires qui n'ont pas été prises en compte lors des phases précédentes ?
- La configuration matérielle/électronique sélectionnée fonctionne-t-elle comme prévu pendant la durée de vie anticipée en conditions réelles ?
Comment l'historique des données a permis d'identifier et de corriger un défaut du dispositif
Le bureau d'études a développé 10 prototypes de pompe à infusion et les a déployés auprès de 10 utilisateurs différents pendant une durée de six semaines. Après la durée des tests, il a été déterminé que trois des 10 prototypes ne détectaient pas efficacement l'occlusion. Au départ, l'équipe a pensé que le capteur était en cause. Lorsque les prototypes ont été retournés au laboratoire pour être analysés, les ingénieurs ont constaté que les capteurs fonctionnaient en réalité comme prévu. Ils ont découvert en revanche que l'adhésif utilisé pour maintenir le capteur en place sur la pompe ne tenait pas aussi bien dans des conditions humides, et affectait le fonctionnement du capteur.
Après une autre série de tests sur le terrain avec un nouvel adhésif, le capteur de force a donné de bons résultats sur tous les prototypes. Grâce à tout le soin apporté par l'équipe à la caractérisation du capteur dès le début du processus, les ingénieurs ont pu identifier cette petite erreur mécanique apparemment sans gravité, mais néanmoins importante.
Design intégré et transfert à la production
Grâce à leur vigilance à chacune des étapes précédentes, les membres de l'équipe sont certains que leur conception fonctionnera comme prévu tout au long du cycle de vie anticipé du produit. Ils ont également obtenu les autorisations réglementaires et sont prêts à finaliser le design et à passer à la production.
Une documentation claire des procédures garantit l'efficacité de la production
Il est impératif de se préoccuper de l'efficacité de la production en série. L'équipe chargée de la conception a donc travaillé en étroite collaboration avec l'équipe chargée de la fabrication pour tenir compte des particularités importantes du processus d'intégration des capteurs et pour garantir la reproductibilité des étapes.
Dans notre exemple, les spécifications comportaient des procédures d'étalonnage/réétalonnage et des méthodes de réglage de la sensibilité et d'autres paramètres.
Le document présenté ici est un exemple de la procédure d'étalonnage documentée par l'équipe de conception.
Transfert de la conception à la production
Le produit est maintenant prêt à être transféré vers la production pour la fabrication destinée aux utilisateurs finaux. À ce stade, le processus d'intégration est terminé. Si des difficultés devaient survenir au cours de cette ultime phase et avoir un impact sur la conception, l'équipe a déjà recueilli des données solides au cours des précédentes étapes en utilisant les produits de développement OEM FlexiForce. Elle dispose donc d'une base de référence qui l'aidera à rationaliser le processus de résolution du problème.
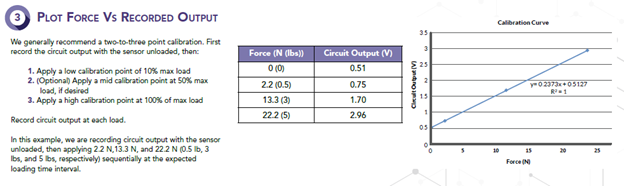
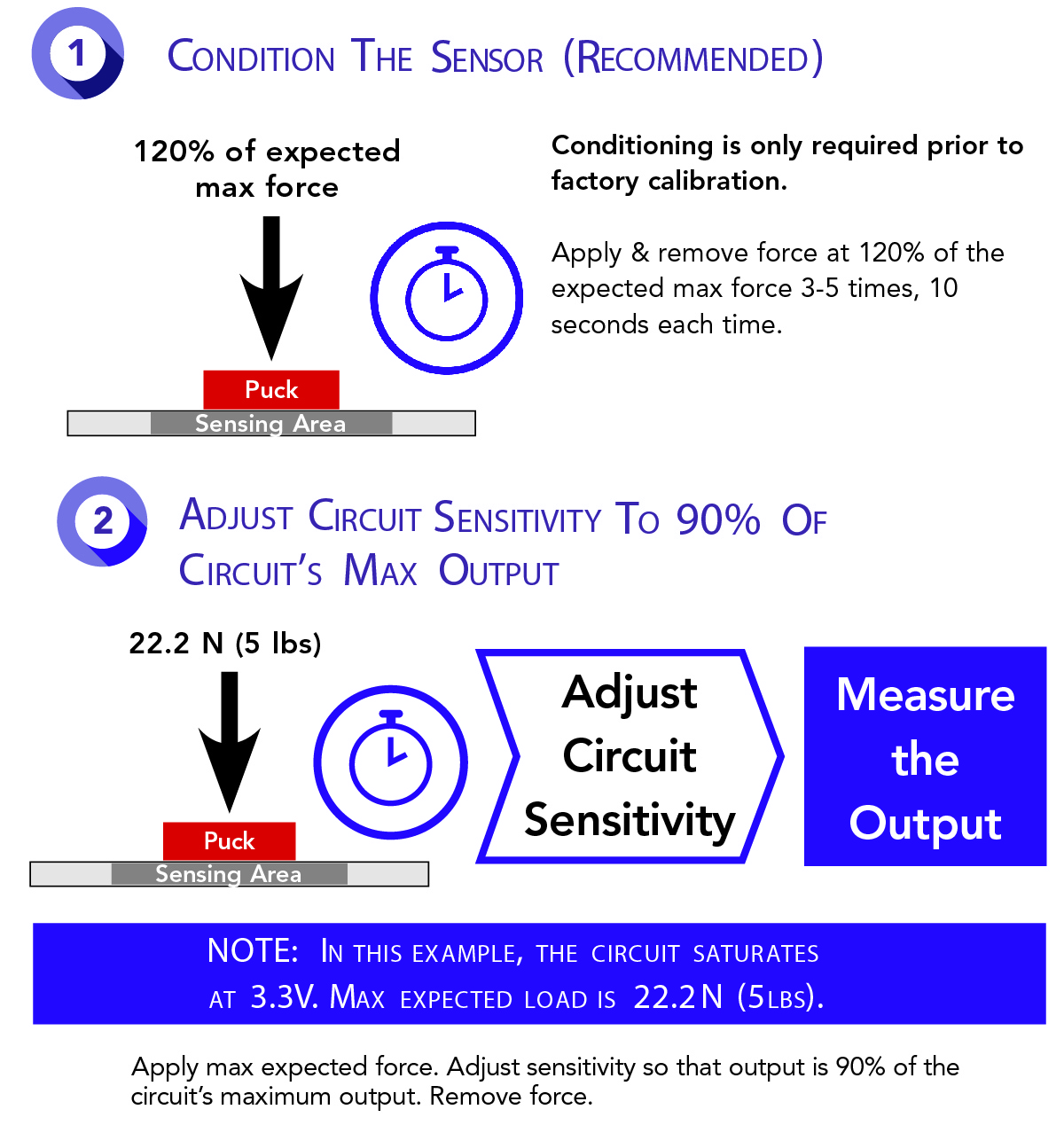